Induction Heating Applications
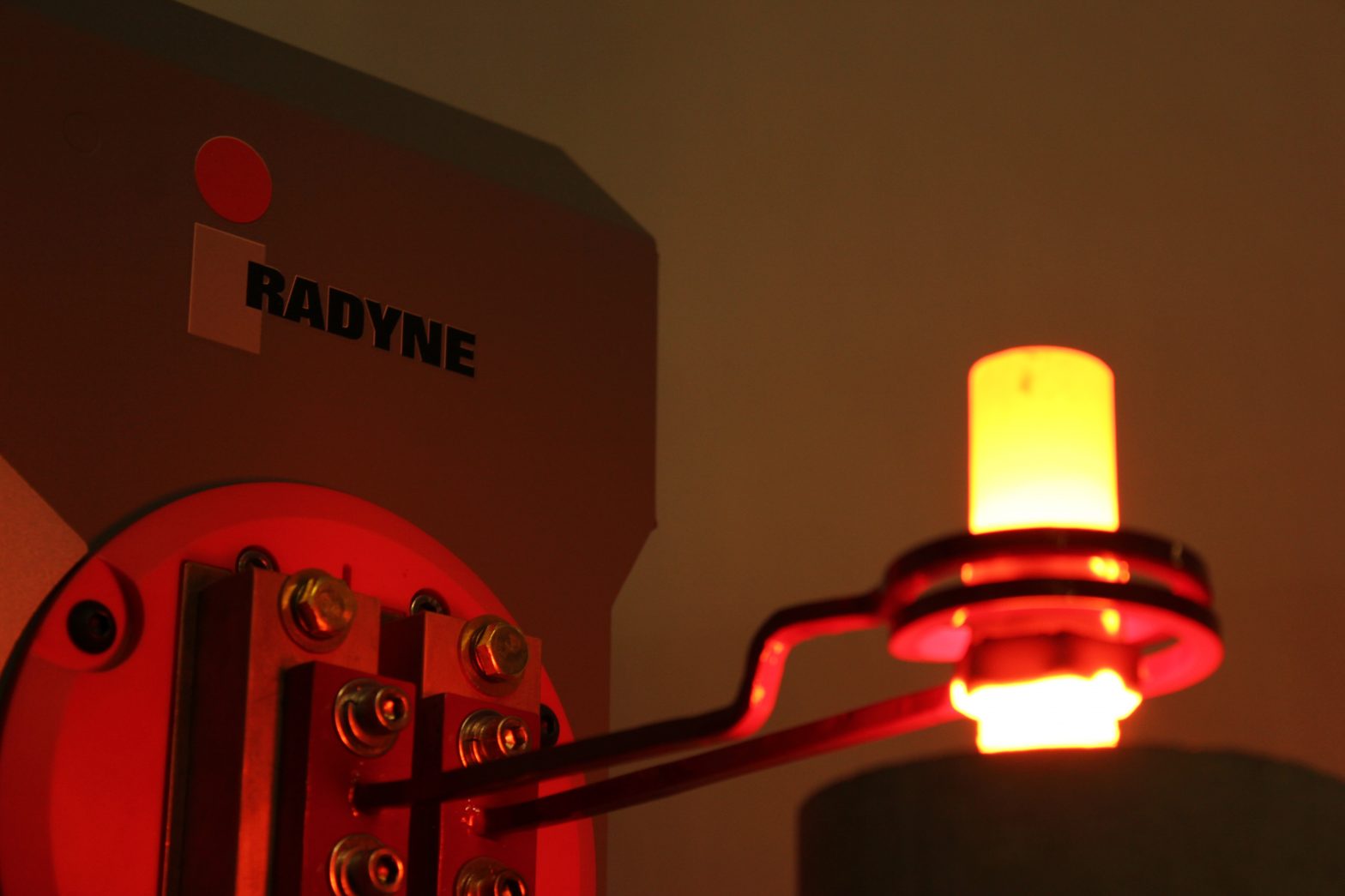
Induction heating technology is flexible and versatile. The ability to heat any conductive material means that induction can be used for a wide range of processes. Induction provides a clean, fast, efficient, and safe alternative to the use of flame torches, infrared, and resistance heaters.
Radyne induction equipment is designed and precision manufactured in Milwaukee, WI using the toughest materials. This means that Radyne equipment is built to last. Our modular designs allow for future updates and expansion of production capabilities as needs change. Our On-site 24/7 service center is on standby to assist with set up, training, and repairs and ensure your production line keeps moving. Our industry-leading Induction Process Engineering Center (IPEC) is able to assist with the necessary feasibility tests as well as make equipment and tooling recommendations
Browse our most common induction heating applications below and discover how Radyne can find solutions for you.
Induction Heating Applications

Hardening
Induction technology opens up new possibilities for hardening and heat-treating procedures. Our inductors can be designed to concentrate the heat within a localized area of a part with extreme accuracy. This makes it possible to harden a specific ware surface without affecting the rest of the part. This allows for the use of less expensive materials while maintaining or improving strength.
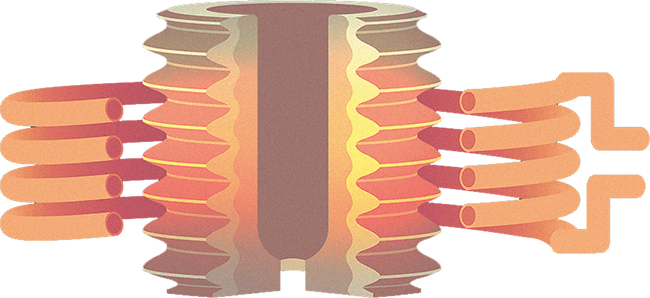
Tempering
Radyne’s induction power supplies can be optionally configured to allow one machine to complete both hardening and tempering processes in one load/unload.
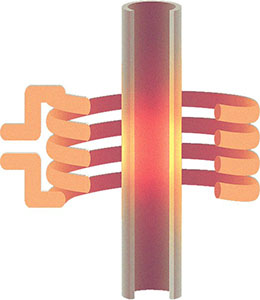
Annealing
Induction Heating Technology presents several distinct advantages for annealing applications. Induction allows for the localized heating of a part. This makes creating consistent and precise annealing profiles possible. Rapid heating made possible by induction technology means that annealing can be done on a continuously moving line and configured to match your line speed.
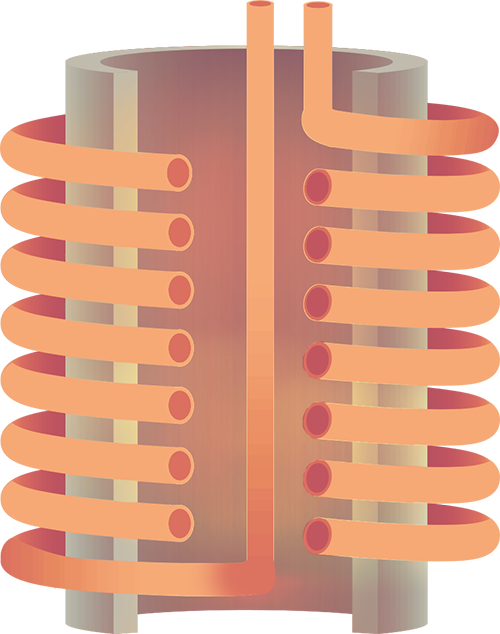
Stress Relieving
Induction heating can be used effectively to selectively stress relieve large sections joined by welding.

Brazing
Manufactures all over the world are switching to brazing with induction rather than an open flame. The many advantages that induction provides make it an ideal solution for the headaches associated with brazing. Induction technology allows for extremely rapid heating times, eliminates the need for complicated ventilation and costly gas cylinders, Improves employee safety, reduces training requirements, and allows for easy integration into your existing production line. Induction also allows for brazing in a controlled atmosphere.
Learn more about Induction Brazing
Soldering
Radyne soldering systems provide clean, repeatable soldering for a wide range of parts.
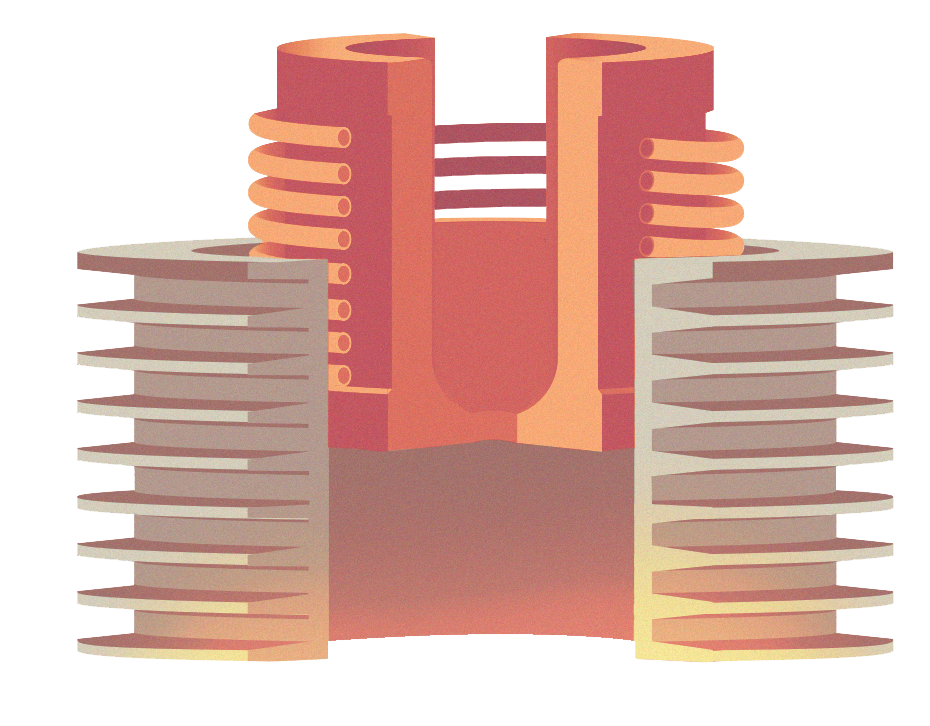
Shrink Fitting
Shrink fitting is an ideal way to join male and female components non-permanently. It involves heating a part to cause expansion, then inserting the joining part and allowing time to cool. This causes the heated part to contract onto the inserted part creating a secure mechanical bond. This technique has become widely used for the fitting of electric motors into housings. Induction is the perfect solution for this process because it makes even and precise heating possible. This is especially important with shrink fitting to make a strong bond and avoid warping the part.
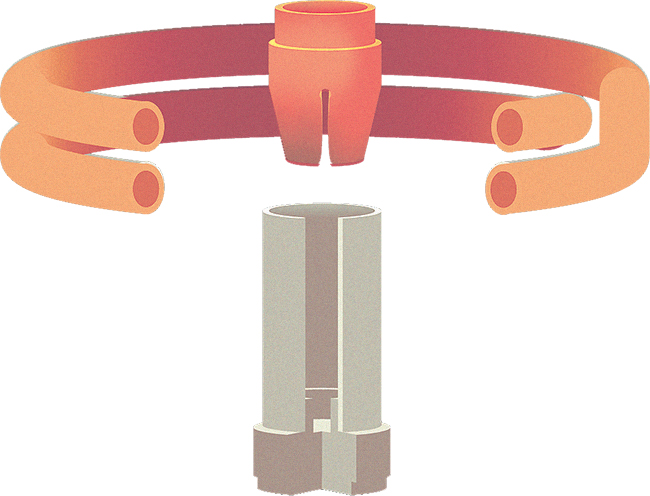
Heat Staking
Heat staking allows for the joining of metallic and plastic components. This is done by heating the metal component and inserting it into a plastic component. This softens the plastic and creates a bond between it and the metallic component. Induction is ideal for this application because it requires the metal component to be heated to a very precise temperature to create a strong enough bond without melting the plastic component too much and damaging the part.

Pipe Heating
Pipe processing requires accurate heating for a number of different reasons. These can include pre-heating before welding or coating, curing coatings, drying moisture, or stress-relieving. Induction provides distinct advantages for weld pre-heating. It allows for the two surfaces to be heated to the exact same temperature with extreme accuracy. This reduces the amount of warping and deformation that can occur as the part cools.
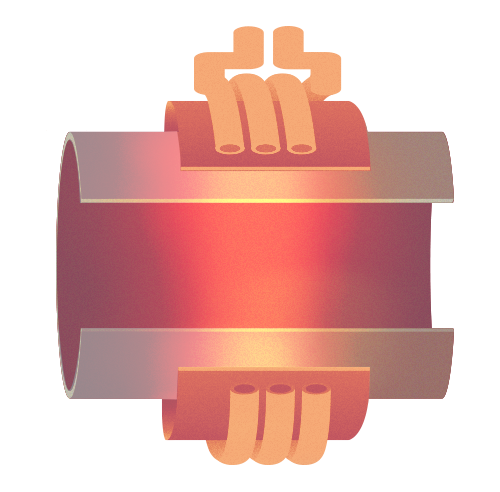
Pipe Coating
Pipe coating is an important step for preventing damage caused by corrosion in harsh environments. Induction makes it possible to pre-heat, coat, and cure coatings all in one step with one machine. The compact nature of induction also allows these systems to be containerized and used aboard offshore vessels or in the field.
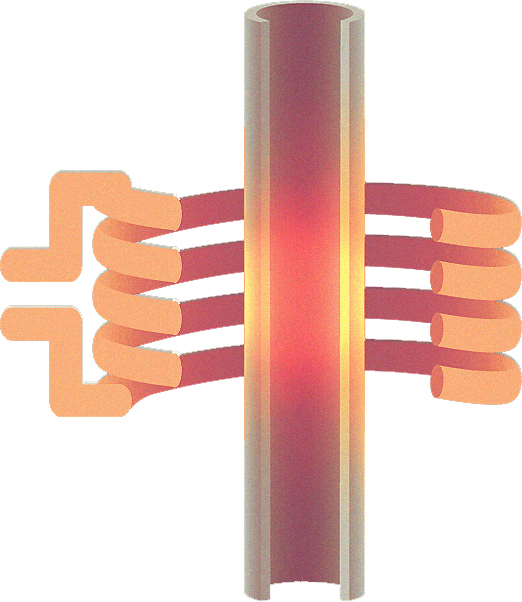
Wire, Rod, Cable, and Tube Processing
Radyne Induction Heating Systems match your mill speed, require minimal maintenance, provide uniform metallurgical quality, and are built for a range of applications from coating and heat treatment.
Learn more about Induction Wire, Rod, Cable, and Tube Processing
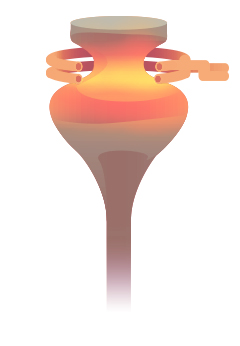
Custom Applications
Radyne’s expertise in induction can be applied to custom applications, ranging from billet heating to susceptor heating and more.