Radyne Services
In addition to providing industry-leading induction equipment, Radyne also offers services to keep that equipment running and up to date.
Radyne Equipment Services
Radyne boasts the industry’s most proficient team of field service engineers. From maintenance and support through to training, we offer a range of equipment services to maintain our customers’ satisfaction.
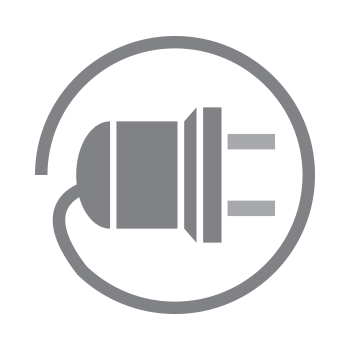
Installation and Startup
Radyne knows how important it is to get your new equipment up and running as quickly as possible. That’s why Radyne engineers are available to help with equipment startup and installation, ensuring that equipment is properly set up to run efficiently and correctly.
To Book Installation and Startup Services Call: 1-414-885-4411
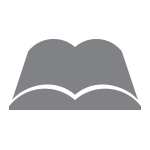
Equipment Training
To ensure our customers get the most use out of our equipment, we have developed a series of training classes for our standard products. These extensive courses cover diagnostic techniques and component replacement procedures that enable customer personnel to efficiently troubleshoot and perform preventive maintenance.
Radyne seminars bring together industry leaders and offer attendees a unique opportunity to network, listen, share and discuss advances in technology, techniques, and business. Help your company minimize downtime by learning how to efficiently troubleshoot and perform preventative maintenance.
Radyne power supply training seminars are an opportunity to learn from industry-leading experts on induction heating technology and equipment, designed to give you the insights you need into diagnostic techniques and component replacement procedures.
To Register for Equipment Training Courses Call: 1-414-885-4411
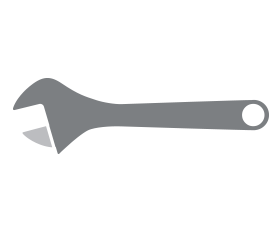
Preventive Maintenance
The best way to ensure downtime is kept to a minimum is to perform necessary preventative maintenance measures. Radyne offers preventive maintenance services to ensure that your system is operating at its best, and to spot potential issues before they force a production interruption.
We’re investing in reducing your downtime with new programs that provide access to loaner induction power supplies for use while your power supply is being repaired.
For Preventative Maintenance Services Call: 1-414-885-4411
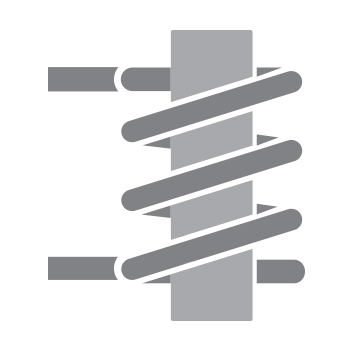
Induction Coils & Tooling
Successful induction heating largely depends on the design and quality of the inductor and quench head that will give the desired profile. Just like other components from a system, coils need infrequent maintenance from normal wear and tear. Radyne can also service damaged inductors.
For Induction Coils & Tooling Call: 1-414-885-4411
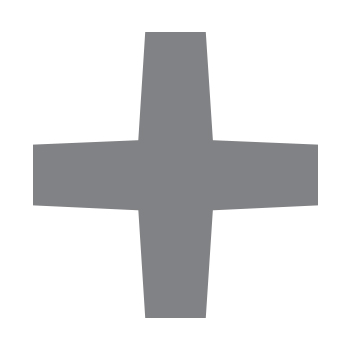
Spare Parts
Radyne maintains a stock inventory of thousands of hard-to-find and long-lead-time components. Parts are available for Radyne and other Inductotherm Group Companies’ induction heating installations. Radyne’s stocked spare parts provide a means of performing maintenance at your convenience, with fast shipment times hedging any unscheduled downtime that might arise in the event of a part failure.
For Spare Parts Call: 1-414-885-4411
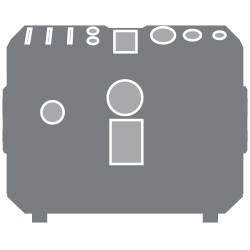
Equipment Refurbishment and Recertification
Remanufactured to exacting standards in our manufacturing facility, Radyne’s refurbished equipment carries a six-month warranty. Our refurbishment technicians evaluate equipment through a rigorous and comprehensive remanufacturing and testing process to deliver Radyne performance, quality, support, and value.
When purchasing from a third party, rest assured that Radyne equipment can be recertified. Through our Legacy Equipment Recertification Program, Radyne’s service engineers ensure equipment is in proper working order and is in compliance with applicable practices.
For Equipment Refurbishment Call: 1-414-885-4411
Learn more about Equipment Refurbishment and Recertification
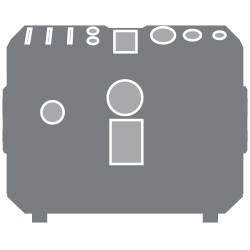
Certified Pre-owned Equipment
From time to time, Radyne has re-certified induction equipment in stock. These units are available for purchase at discounted prices or available for rent.
Radyne’s refurbished equipment carries a six-month warranty. Our refurbishment technicians evaluate equipment through a rigorous and comprehensive testing process to deliver Radyne performance, quality, support, and value.
For Certified Pre-Owned Equipment Call: 1-414-885-4411
Induction Process Engineering Center (IPEC) Services
Radyne’s Induction Process Engineering Center (IPEC) offers the expertise of engineers, metallurgists, and scientists who assure reliable and efficient performance for customized induction heating applications.
With the assistance of IPEC’s engineers, metallurgists and scientists, our customers are able to verify the process and induction heating quality of their part prior to the purchase of a Radyne induction system. The IPEC team works with our customers to map their process, recommend changes and conduct practical heating tests on sample components.
Located in Radyne’s 30,000-plus sq. ft. engineering and manufacturing facility, IPEC includes advanced super-computer modeling and simulation of induction heating processes and equipment, a metallurgical laboratory, an induction heating laboratory, and an induction tooling design center to deliver the exacting results of our customers expect.
Radyne’s application engineers, materials scientists, and metallurgists bring unparalleled capabilities for new process development.
Click to learn more about IPEC
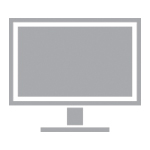
Applications Engineering Consultation
As part of Radyne’s Induction Process Engineering Center, Radyne staffs a team of application engineers dedicated to designing a process that matches your specific application. For your specific needs, Radyne has made our team of experts available for independent consultation on your application. Leverage over 75 years of induction heating experience and innovation by consulting with our team of skilled applications engineers.
With specialists in wire, stainless steel, aluminum brazing, and shrink fitting, Radyne has the experience and manpower to tackle the most challenging heating projects.
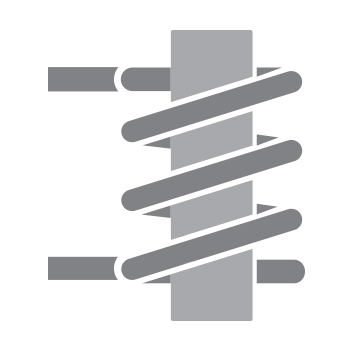
Induction Tooling Design and Development
Successful induction heating depends on the design and quality of the Inductor (aka Induction Coil), Quench, Part Nest Tooling, Materials employed, and the Process Parameters that will give the desired profile. These are tailored to the specific part per its material properties and geometry. As part of Radyne’s Induction Process Engineering Center, we offer customized induction tooling design and development services.
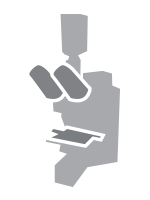
Metallurgical Analysis
Our metallurgical laboratory includes experienced and highly skilled practitioners who use state-of-the-art lab equipment to ensure quality craftsmanship at all levels of your product’s life cycle. Radyne’s experience in designing processes achieving specific metallurgy in your part is a critical component of the Induction Process Engineering Center.
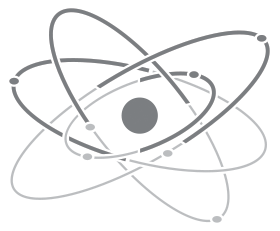
Process Engineering and Development
Radyne’s mathematics prowess enables advanced techniques for modeling heat treating and other processes that ensure accurate, controlled case depth patterns with the part properties you need to dominate in your market space. Radyne investigates your current part properties and your requirements to create a tailored process for maximum efficiency.
As part of Radyne’s Induction Process Engineering Center, Radyne staffs a team of application engineers dedicated to designing a process that matches your specific application. With specialists in many applications, Radyne is your one-stop destination.