Annealing With Induction
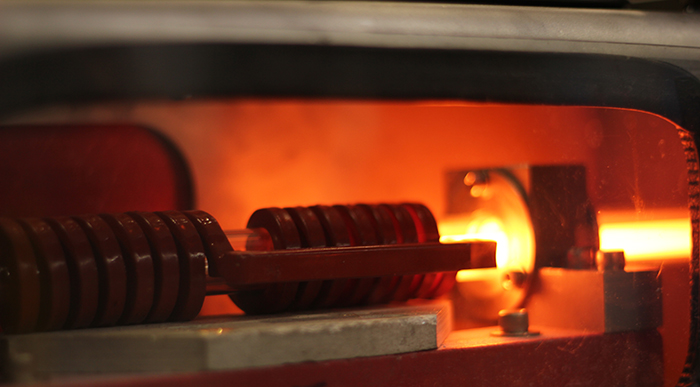
What Is Annealing?
Annealing is a metal treatment process designed to alleviate stresses and tensions that may arise from various manufacturing procedures. This is crucial to prevent warping or cracking of the metal component during its operational lifespan or subsequent manufacturing operations. The annealing process comprises three distinct stages. First is the Recovery Stage, during which the material is heated to a temperature that relieves internal stresses. Following this is the Recrystallization Stage, where the material is held at the Recrystallization Temperature for a sufficient duration to facilitate the formation of new grains. It’s worth noting that certain metals, like steel, may not exhibit this stage. Finally, in the Grain Growth Stage, the material is gradually cooled, allowing sufficient time for the development of new grains. The rate of cooling directly influences the rate of grain growth.
Advantages of Annealing With Induction
Annealing, when conducted in a conventional furnace, involves subjecting parts to heat for a sufficient duration to reach the desired temperature, maintaining that temperature, and then gradually allowing the parts to cool under controlled conditions. In many instances, this necessitates the transfer of parts between multiple furnaces for the various heating, holding, and cooling stages.
However, induction heating technology offers a transformative approach to the annealing process. Induction enables the annealing of parts in a continuously moving line at high speeds. This method is applicable to individual parts like bullet casings or integrated into a mill for wire or tube drawing. By eliminating the bottleneck created by furnaces in the production line, manufacturers gain greater flexibility in controlling line speed and reduce downtime in other process stages.
The rapidity of induction heating is a key advantage. Induction coils for annealing can be much shorter compared to furnaces or infrared tunnels. This is particularly advantageous in continuous annealing operations, where induction heating allows for plant layouts that significantly save floor space.
Localized Induction Annealing
Induction technology facilitates the practice of localized annealing, where only specific portions of a part undergo annealing while the rest retain their hardness. Manufacturers find this capability valuable because it allows them to selectively anneal areas that need increased ductility without compromising the existing work hardening in other sections. This technique is frequently applied in the production of ammunition and tools.
Induction Annealing in a Controlled Atmosphere
Induction annealing is frequently conducted without the need for a controlled atmosphere. This is feasible because induction heating typically takes only seconds, effectively annealing the part before oxides have a chance to form. Nevertheless, certain processes may still demand a controlled atmosphere, and this is where induction technology excels. Induction generates heat in a part by inducing a current using a magnetic field, and this magnetic field can penetrate materials such as quartz, glass, various plastics, and more. Consequently, achieving controlled atmosphere heating becomes remarkably straightforward, as the inductor coil can be positioned outside of the atmosphere chamber. Furthermore, induction technology allows controlled atmosphere annealing to be carried out seamlessly on a continuously moving line.