Induction Process Engineering Center
Induction Process Engineering Center (IPEC)
Radyne Induction Process Engineering Center (IPEC) offers the expertise of engineers, metallurgists, scientists, and technicians who adapt Radyne Induction heating processes to achieve the results required from our customers.
With the assistance of IPEC’s talented team, our customers are able to validate the quality of the induction heating process or heat treatment of their components prior to the purchase of Radyne induction heating systems. The IPEC team works with clients to analyze their requirements, existing processes, and results to recommend high-return improvements utilizing induction heating. The IPEC also conducts induction heating process feasibility demonstrations on customer-supplied components along with metallurgical and other studies for customer evaluation.
IPEC is located in Radyne’s 40,000 + sq.ft. Milwaukee WI engineering and manufacturing facility. Capabilities include computer analysis utilizing finite element modeling (FEM) for reliable mathematical estimations, a fully equipped metallurgical and induction heating laboratory, and an induction tooling design center. Radyne’s talented team of application engineers, material scientists, metallurgists, technicians, machinists, and coil makers work together to confront the challenges of new process development. The IPEC gives our customers peace of mind by demonstrating that the system they order is capable of achieving their desired results.
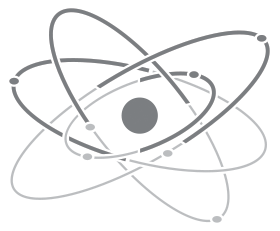
The Radyne IPEC excels in the development of:
- Cutting Edge Inductor and Susceptor Designs
- Eco-Friendly, Ultra-High Efficiency, Green Inductor Design
- Vacuum and Controlled Atmosphere Induction Processes
- Development of Precise Induction Heating and Hardening profiles
- Advanced Thermal and Magnetic Modeling, Simulation, and numerical predictions with Finite and Boundary Element Analysis
- Brazing and Soldering Techniques for a wide range of metals and hard to braze parts
Equipment Capabilities
Radyne is equipped with a fully radiometric thermal imager with visual and thermal composite image functionality. We perform prototype heat treatment on parts with over a dozen of our own processing machines, using machining & tooling that is similar or identical to those which are shipped to our customers for production.
- Hardness testers
- Metallography systems
- Image analyzers
- Carbon sulfur analyzers
- Specialized instruments
- Cut-off saws
- 12 induction heating machines
- Radiometric Thermal Imager
- Controlled Atmosphere and Vacuum Processing
Radyne and our partner Inductotherm Group companies bring together the world’s leading experts and researchers worldwide to solve the most challenging process problems for our customers. We have networked and video-conference connected laboratory facilities located domestically in New Jersey, Connecticut, Massachusetts, Wisconsin, Ohio, Pennsylvania, Michigan, and New York, and internationally in Ontario, Germany, Belgium, England, Scotland, France, India, Mexico, Australia, Japan, Korea, China, Brazil, Taiwan, Turkey, and Spain.
When you need the best, come to Radyne and the globally united Inductotherm Group of companies. Come to the team that is passionate about lean manufacturing processes, the innovative R&D group at Radyne and the Inductotherm Group.
Learn more about Inductotherm Group
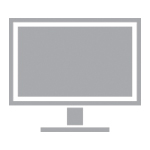
Applications Engineering Consultation
As part of Radyne’s Induction Process Engineering Center, Radyne staffs a team of application engineers dedicated to designing a process that matches your specific application. For your specific needs, Radyne has made our team of experts available for independent consultation on your application. Leverage over 75 years of induction heating experience and innovation by consulting with our team of skilled applications engineers.
With specialists in wire, stainless steel, aluminum brazing, and shrink fitting, Radyne has the experience and manpower to tackle the most challenging heating projects.
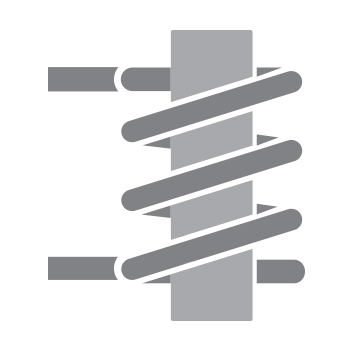
Induction Tooling Design and Development
Successful induction heating depends on the design and quality of the Inductor (aka Induction Coil), Quench, Part Nest Tooling, Materials employed, and the Process Parameters that will give the desired profile. These are tailored to the specific part per its material properties and geometry. As part of Radyne’s Induction Process Engineering Center, we offer customized induction tooling design and development services.
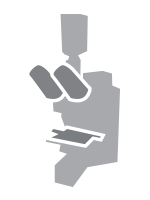
Metallurgical Analysis
Our metallurgical laboratory includes experienced and highly skilled practitioners who use state-of-the-art lab equipment to ensure quality craftsmanship at all levels of your product’s life cycle. Radyne’s experience in designing processes and achieving specific metallurgy in your part is a critical component of the Induction Process Engineering Center.
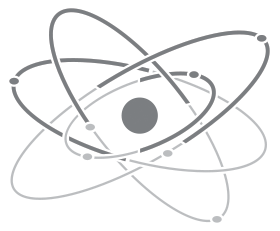
Process Engineering and Development
Radyne’s mathematics prowess enables advanced techniques for modeling heat treating and other processes that ensure accurate, controlled case depth patterns with the part properties you need to dominate in your market space. Radyne investigates your current part properties and your requirements to create a tailored process for maximum efficiency.
As part of Radyne’s Induction Process Engineering Center, Radyne staffs a team of application engineers dedicated to designing a process that matches your specific application. With specialists in many applications, Radyne is your one-stop destination.